In the world of electronics, the complexity of projects continues to evolve, requiring both hobbyists and professionals to stay updated with the latest tools and technologies. Whether you’re building a sophisticated robotics system, developing an industrial automation setup, or simply tinkering with gadgets at home, certain components and interfaces are fundamental. In this article, we’ll delve into four crucial elements: the Ethernet I/O controller, the RC simulator interface, the USB stepper motor controller, and the stepper motor driver manual.
Each of these components plays a pivotal role in ensuring the seamless operation of electronic systems. The Ethernet I/O controller enables efficient communication between devices over a network, essential for automation and remote control. The RC simulator interface is indispensable for enthusiasts working with radio-controlled systems, allowing for accurate simulation and testing. The USB stepper motor controller is a critical tool for precision control in motion-based projects, providing an easy interface for motor management. Lastly, the stepper motor driver manual is a guide that ensures the correct installation and operation of stepper motors, which are vital in a wide range of applications.
Throughout this article, we’ll explore these components in detail, discussing their functions, applications, and how they interconnect within a broader electronics framework. Whether you’re a seasoned engineer or a beginner looking to expand your knowledge, understanding these tools will enhance your ability to design and execute advanced electronic projects.
Ethernet I/O Controller: The Backbone of Networked Communication
An Ethernet I/O controller is a crucial component in modern electronics, especially in systems that require reliable and efficient communication across various devices. This controller acts as an interface that allows input and output (I/O) signals to be transmitted over an Ethernet network, making it an integral part of industrial automation, remote monitoring, and smart home systems.
The primary function of an Ethernet I/O controller is to convert data from various sensors, actuators, and other devices into Ethernet packets that can be transmitted over a network. This capability is particularly valuable in environments where multiple devices need to communicate with a central processing unit or with each other. For instance, in an industrial setting, an Ethernet I/O controller can manage data from temperature sensors, pressure gauges, and machinery controls, ensuring that all components work harmoniously.
One of the key advantages of using an Ethernet I/O controller is its scalability. As your project grows, adding more devices or expanding the network can be done with minimal disruption. The controller’s ability to handle multiple I/O points simultaneously ensures that even complex systems can operate efficiently. Moreover, the use of standard Ethernet protocols means that the system can be easily integrated with other networked devices, making it a versatile choice for various applications.
Another important aspect of Ethernet I/O controllers is their role in enhancing system reliability. By facilitating real-time communication and data exchange, these controllers help prevent bottlenecks and ensure that all parts of the system are functioning optimally. This reliability is critical in applications where downtime can lead to significant losses, such as in manufacturing or critical infrastructure.
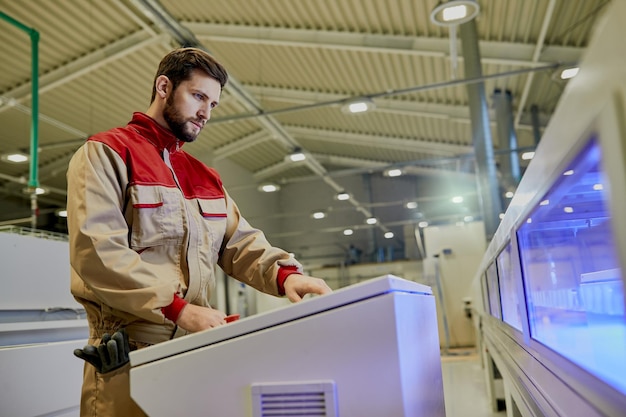
In summary, an Ethernet I/O controller is essential for any project that requires robust and flexible networked communication. Its ability to seamlessly integrate multiple devices and ensure reliable data transmission makes it a cornerstone of modern electronics systems.
RC Simulator Interface: Bridging the Gap Between Virtual and Real-World Control
The RC simulator interface is a vital tool for anyone involved in the world of radio-controlled (RC) systems, whether you’re a hobbyist, a professional pilot, or an engineer testing new designs. This interface serves as the bridge between your physical RC transmitter and a virtual simulation environment, allowing you to practice and refine your control skills without the risks or costs associated with real-world flights or maneuvers.
At its core, the RC simulator interface converts the signals from your RC transmitter into a format that can be interpreted by simulation software. This process enables the simulator to accurately mimic the behavior of an RC vehicle—be it an airplane, helicopter, drone, or car—based on your inputs. The interface ensures that every stick movement, throttle adjustment, and control tweak you make on the transmitter is faithfully replicated in the simulation, providing a realistic training experience.
One of the primary benefits of using an RC simulator interface is the ability to hone your skills in a controlled environment. Whether you’re learning the basics of RC piloting or mastering advanced maneuvers, the simulator interface allows you to practice without fear of crashing expensive models. This is particularly beneficial for beginners who can experiment with different scenarios and build confidence before taking their skills to the field.
Furthermore, an RC simulator interface is invaluable for testing and fine-tuning new models or custom modifications. Before committing to a build, you can use the simulator to observe how your design behaves under various conditions, saving time and resources. Engineers and designers often rely on these interfaces to validate concepts and make necessary adjustments before physical testing.
In addition to skill development and testing, the RC simulator interface also offers convenience. Many modern interfaces are plug-and-play, requiring minimal setup, and are compatible with a wide range of transmitters and simulation software. This ease of use makes it accessible to a broad audience, from casual enthusiasts to seasoned professionals.
Overall, the RC simulator interface is an indispensable tool that enhances the RC experience by providing a safe, cost-effective, and flexible platform for practice and testing. Whether you’re aiming to improve your piloting skills or experiment with new designs, this interface is the key to unlocking your full potential in the world of RC systems.
USB Stepper Motor Controller: Precision Control Made Easy
A USB stepper motor controller is an essential tool for anyone involved in projects that require precise control of stepper motors. Whether you’re working on a 3D printer, CNC machine, or any other motion-based system, this controller provides a straightforward way to manage and fine-tune motor movements via a computer’s USB interface.
The primary function of a USB stepper motor controller is to convert digital commands from a computer into precise electrical pulses that drive the stepper motor. These pulses control the motor’s position, speed, and direction with high accuracy, making it ideal for applications where precision is crucial. By using a USB interface, the controller allows for easy connectivity and control, enabling users to program and adjust motor parameters directly from their computer.
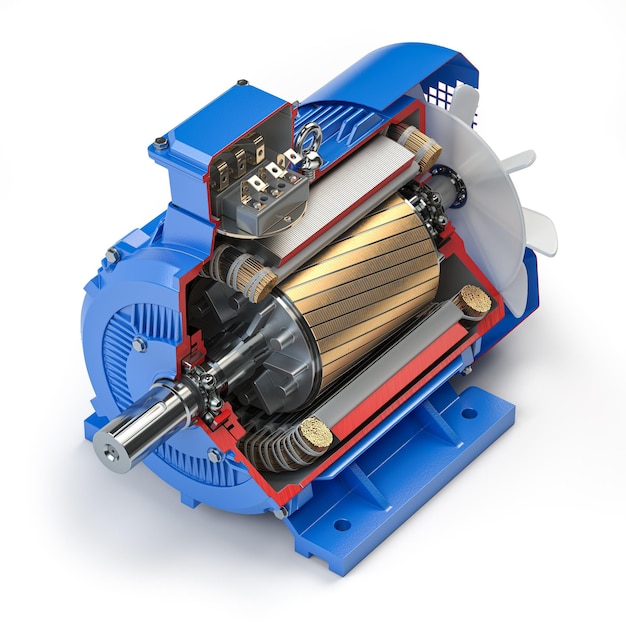
One of the significant advantages of using a USB stepper motor controller is its ease of use. The plug-and-play nature of USB devices means that setting up the controller typically requires no more than connecting it to your computer and installing the necessary drivers or software. This simplicity makes it accessible even to those who may not have extensive experience with electronics or motor control systems.
Moreover, a USB stepper motor controller offers extensive customization options. Users can configure various parameters such as step resolution, acceleration, deceleration, and maximum speed, allowing for tailored control to meet the specific needs of their project. This flexibility is particularly valuable in applications like robotics, where precise motor control can make the difference between success and failure.
Another key benefit of a USB stepper motor controller is its ability to integrate with software for automation and complex motion tasks. Many controllers come with software that supports scripting and automation, enabling users to create intricate motion sequences and execute them with precision. This capability is essential for projects that require repetitive tasks, such as assembly lines, or for creating detailed, repeatable movements in artistic installations.
In addition, USB stepper motor controllers are often compact and portable, making them suitable for both desktop and field use. Their versatility and convenience make them a popular choice among makers, engineers, and hobbyists alike.
In summary, a USB stepper motor controller provides a powerful and user-friendly solution for managing stepper motors with precision and ease. Its straightforward setup, extensive customization options, and integration capabilities make it an invaluable tool for a wide range of motion control projects.
Stepper Motor Driver Manual: Your Guide to Effective Motor Management
The stepper motor driver manual is an indispensable resource for anyone working with stepper motors, whether you’re an engineer designing complex machinery or a hobbyist building a DIY project. This manual provides crucial information on how to properly install, configure, and operate stepper motor drivers, ensuring optimal performance and longevity of your motors.
A stepper motor driver is responsible for controlling the electrical pulses that drive the stepper motor, allowing for precise control over its position and movement. The driver takes commands from a controller and translates them into electrical signals that step the motor in discrete increments. Understanding the functionality and settings detailed in the stepper motor driver manual is essential for achieving accurate and reliable motor performance.
The manual typically includes sections on wiring diagrams, setup procedures, and troubleshooting tips. Wiring diagrams are particularly important as they illustrate how to connect the driver to the motor, power supply, and controller. Proper wiring is crucial to avoid damage and ensure the driver operates correctly. The setup section guides users through configuring the driver’s parameters, such as step resolution, current limits, and microstepping modes. Accurate setup is vital for matching the driver’s capabilities with the motor’s specifications and the project’s requirements.
Another key aspect covered in the stepper motor driver manual is calibration and tuning. The manual often provides guidelines for adjusting settings to optimize motor performance, including speed, torque, and accuracy. Proper calibration can significantly enhance the efficiency and effectiveness of your motor-driven system, making it a critical part of the setup process.
Troubleshooting information is also a valuable component of the manual. Common issues such as overheating, erratic movements, or connectivity problems can be diagnosed and resolved using the troubleshooting tips provided. This section helps users address problems quickly and maintain the reliability of their systems.
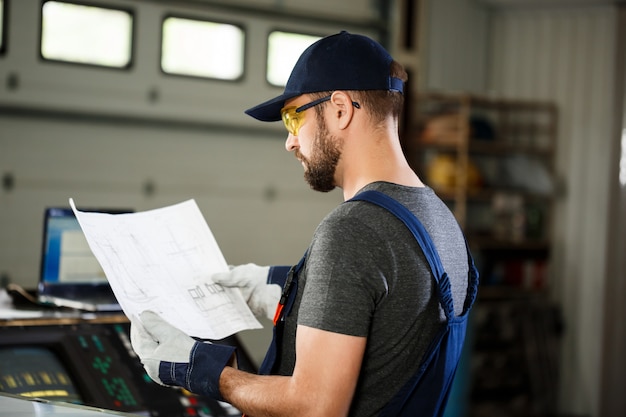
Furthermore, the manual may include safety precautions and maintenance recommendations to ensure safe operation and extend the lifespan of the driver and motor. Regular maintenance, such as checking for loose connections and cleaning components, helps prevent failures and maintains consistent performance.
In summary, the stepper motor driver manual is a comprehensive guide that provides essential information for the effective management of stepper motors. By following the instructions and recommendations in the manual, users can ensure proper installation, configuration, and maintenance, leading to optimal motor performance and reliability in their projects.
Conclusion
In the realm of advanced electronics and automation, understanding the tools and components that drive your projects is crucial. We’ve explored four key elements: the Ethernet I/O controller, RC simulator interface, USB stepper motor controller, and stepper motor driver manual. Each of these components plays a distinct yet interconnected role in ensuring the seamless operation of modern electronic systems.
The Ethernet I/O controller facilitates robust communication across networked devices, essential for automation and remote control applications. Its ability to handle multiple I/O points and integrate with various devices makes it a backbone of networked systems.
The RC simulator interface provides a bridge between physical RC transmitters and virtual simulation environments, offering a safe and cost-effective platform for skill development and design testing. This tool is invaluable for both beginners and professionals in the RC community, allowing for realistic practice and experimentation.
The USB stepper motor controller simplifies precise motor management by converting digital commands from a computer into accurate motor movements. Its user-friendly setup and extensive customization options make it a popular choice for projects requiring exact control, from 3D printing to robotics.
Lastly, the stepper motor driver manual is a comprehensive guide that ensures proper installation, configuration, and maintenance of stepper motor drivers. By providing detailed information on wiring, calibration, and troubleshooting, this manual helps users achieve optimal performance and reliability in their motor-driven systems.
Together, these components and resources form a cohesive toolkit for tackling complex electronic projects. Mastering their use enhances your ability to design, control, and innovate within the electronics field. Whether you’re working on industrial automation, RC systems, or precision motion control, understanding and effectively utilizing these tools will significantly contribute to your project’s success.
Read also: