Understanding Stepper Motor Drivers, Modbus Stepper Drivers, Stepper Motor Current, and Slip Ring Testing: A Comprehensive Guide
Stepper motors are integral components in various automation and control systems, offering precise control of angular position without the need for feedback systems. They are widely used in industrial applications, 3D printers, CNC machines, and robotics. However, the performance and efficiency of stepper motors depend on several factors, including the stepper motor driver, Modbus stepper driver, stepper motor current, and slip ring testing.
A stepper motor driver is essential for controlling the power sent to the motor phases, thereby dictating the motor’s rotation and positioning accuracy. In some applications, a Modbus stepper driver enhances communication and control through a standardized protocol, allowing multiple devices to interact seamlessly. Meanwhile, the stepper motor current is crucial for determining the torque and speed of the motor, directly impacting its efficiency and performance. Lastly, slip ring testing is vital in applications where continuous rotation is required, ensuring uninterrupted electrical connections.
In this article, we will delve deeper into each of these topics, explaining their importance, how they work, and their interconnections. Whether you’re an engineer, a hobbyist, or someone looking to understand more about these technologies, this comprehensive guide will equip you with the knowledge needed to optimize the performance of your stepper motor systems.
Understanding Stepper Motor Drivers
A stepper motor driver is a critical component in the operation of stepper motors, as it controls the electrical signals that dictate the motor’s movement. Essentially, the stepper motor driver acts as an interface between the motor and the control system, ensuring that the motor receives the correct amount of current and the appropriate timing for precise motion.
How Stepper Motor Drivers Work
Stepper motor drivers operate by converting digital pulses from a controller into electrical current that is sent to the motor windings. Each pulse moves the motor a specific step, which allows for precise control of its position and speed. The driver manages the power supply to the motor phases, and its primary function is to sequence these currents correctly to achieve accurate positioning.
Types of Stepper Motor Drivers
There are various types of stepper motor drivers, including unipolar and bipolar drivers. Unipolar drivers have a center tap on the motor winding, which simplifies the driver design but may result in lower torque. Bipolar drivers, on the other hand, do not have a center tap and can provide higher torque and efficiency. The choice between these types depends on the specific requirements of the application.
Key Features of Stepper Motor Drivers
When selecting a stepper motor driver, several key features should be considered:
Microstepping Capabilities: Many modern drivers offer microstepping, which allows for smoother motion and greater precision by subdividing each full step into smaller increments. Current Limiting: This feature protects the motor from overheating by limiting the amount of current supplied to it, ensuring reliable performance and longevity. Voltage Rating: The driver must be compatible with the voltage requirements of the stepper motor to avoid damage and ensure efficient operation.
The Impact on Motor Performance
The performance of a stepper motor is heavily influenced by the driver’s characteristics. A high-quality stepper motor driver can significantly enhance the motor’s efficiency, reduce noise and vibrations, and improve overall accuracy. Properly configuring the driver settings, such as current limit and microstepping resolution, is crucial for achieving optimal performance.

In summary, the stepper motor driver plays a vital role in the functionality of stepper motors. By converting digital pulses into precise control signals, it enables accurate and reliable motor operation. Understanding the different types of drivers and their features is essential for optimizing motor performance and ensuring the success of your automation projects.
Exploring Modbus Stepper Drivers
Modbus stepper drivers combine the functionality of traditional stepper motor drivers with the robust Modbus communication protocol. This integration allows for enhanced control and coordination in complex automation systems, making it an ideal choice for applications requiring networked devices and centralized control.
What is a Modbus Stepper Driver?
A Modbus stepper driver is a type of stepper motor driver that uses the Modbus protocol for communication. Modbus is a serial communication protocol widely used in industrial automation to facilitate communication between various devices and control systems. By incorporating Modbus, these drivers enable seamless integration with Modbus-compatible systems, allowing for efficient data exchange and control.
Benefits of Using Modbus Stepper Drivers
- Centralized Control: One of the main advantages of Modbus stepper drivers is their ability to connect multiple drivers to a single control system. This centralized approach simplifies the management of complex systems with multiple stepper motors, improving overall system efficiency and ease of operation.
- Real-Time Monitoring and Diagnostics: Modbus communication allows for real-time monitoring of stepper motor performance and driver status. This capability provides valuable diagnostic information, such as error codes and performance metrics, which can be used to troubleshoot issues and optimize motor performance.
- Flexibility and Scalability: Modbus stepper drivers offer flexibility in terms of system design and scalability. As your system grows or evolves, Modbus allows for easy addition or modification of devices without significant changes to the existing infrastructure.
How Modbus Stepper Drivers Work
Modbus stepper drivers operate by receiving commands from a Modbus master device, such as a programmable logic controller (PLC) or a computer. These commands are transmitted over a Modbus network, instructing the driver on how to control the stepper motor. The driver then translates these commands into the appropriate electrical signals for the motor.
Integration with Automation Systems
In automated systems, Modbus stepper drivers can be integrated with other Modbus-compatible devices, such as sensors and actuators. This integration facilitates coordinated control across the entire system, enabling complex processes to be managed efficiently and with high precision.
Choosing the Right Modbus Stepper Driver
When selecting a Modbus stepper driver, consider the following factors:
Compatibility: Ensure that the driver is compatible with your existing Modbus network and control systems.
Communication Speed: The speed of communication can affect the performance of your system. Choose a driver that meets your speed requirements.

Configuration Options: Look for drivers that offer flexible configuration settings to match the specific needs of your application.
In conclusion, Modbus stepper drivers offer significant advantages in terms of centralized control, real-time monitoring, and system scalability. By leveraging the Modbus protocol, these drivers enable more efficient and effective management of stepper motors in complex automation systems. Understanding their features and benefits will help you make informed decisions and optimize your system’s performance.
Managing Stepper Motor Current
Stepper motor current is a crucial parameter in optimizing the performance and longevity of stepper motors. Understanding and managing this current is essential for achieving the desired torque, speed, and efficiency in your automation systems.
The Importance of Stepper Motor Current
Stepper motors operate based on the current supplied to their windings. The amount of current determines the motor’s torque and overall performance. Insufficient current can lead to reduced torque and sluggish performance, while excessive current can cause overheating and potential damage to the motor. Proper management of stepper motor current is therefore vital for ensuring reliable and efficient motor operation.
How Stepper Motor Current Affects Performance
Torque Production: The primary function of stepper motor current is to generate torque. Higher current levels result in greater torque, which is necessary for moving heavy loads or achieving precise positioning. However, it’s important to balance this with the risk of overheating and reduced motor lifespan.
Heat Generation: Increased current levels lead to higher heat generation within the motor. Excessive heat can degrade the motor’s insulation and bearings, leading to premature failure. Effective cooling and proper current management are essential to mitigate these risks.
Efficiency and Power Consumption: The efficiency of a stepper motor is influenced by the current supplied to it. Running the motor at higher currents increases power consumption, which may not always be necessary for all applications. Optimizing the current to match the specific requirements of your application can help reduce power consumption and improve overall efficiency.
Setting the Correct Stepper Motor Current
To set the correct stepper motor current, consider the following steps:
Consult Motor Specifications: Refer to the motor’s datasheet to determine the recommended current settings. This information will provide guidelines on safe operating ranges and maximum allowable currents.
Adjust Driver Settings: Many stepper motor drivers allow for current adjustment via dip switches, potentiometers, or digital settings. Properly configuring these settings based on your motor’s requirements is crucial for achieving optimal performance.
Monitor and Test: Regularly monitor the motor’s temperature and performance to ensure that the current settings are appropriate. Testing different current levels under operational conditions can help fine-tune the settings for the best balance between performance and heat generation.
Common Issues and Solutions
Overheating: If the motor overheats, it may be due to excessive current. Reduce the current setting or improve cooling to address this issue.
Insufficient Torque: If the motor struggles to move the load, increase the current within safe limits to enhance torque production.
Inconsistent Performance: Fluctuations in current settings or improper driver configuration can lead to inconsistent motor behavior. Ensure that the driver settings are stable and correctly aligned with the motor’s specifications.
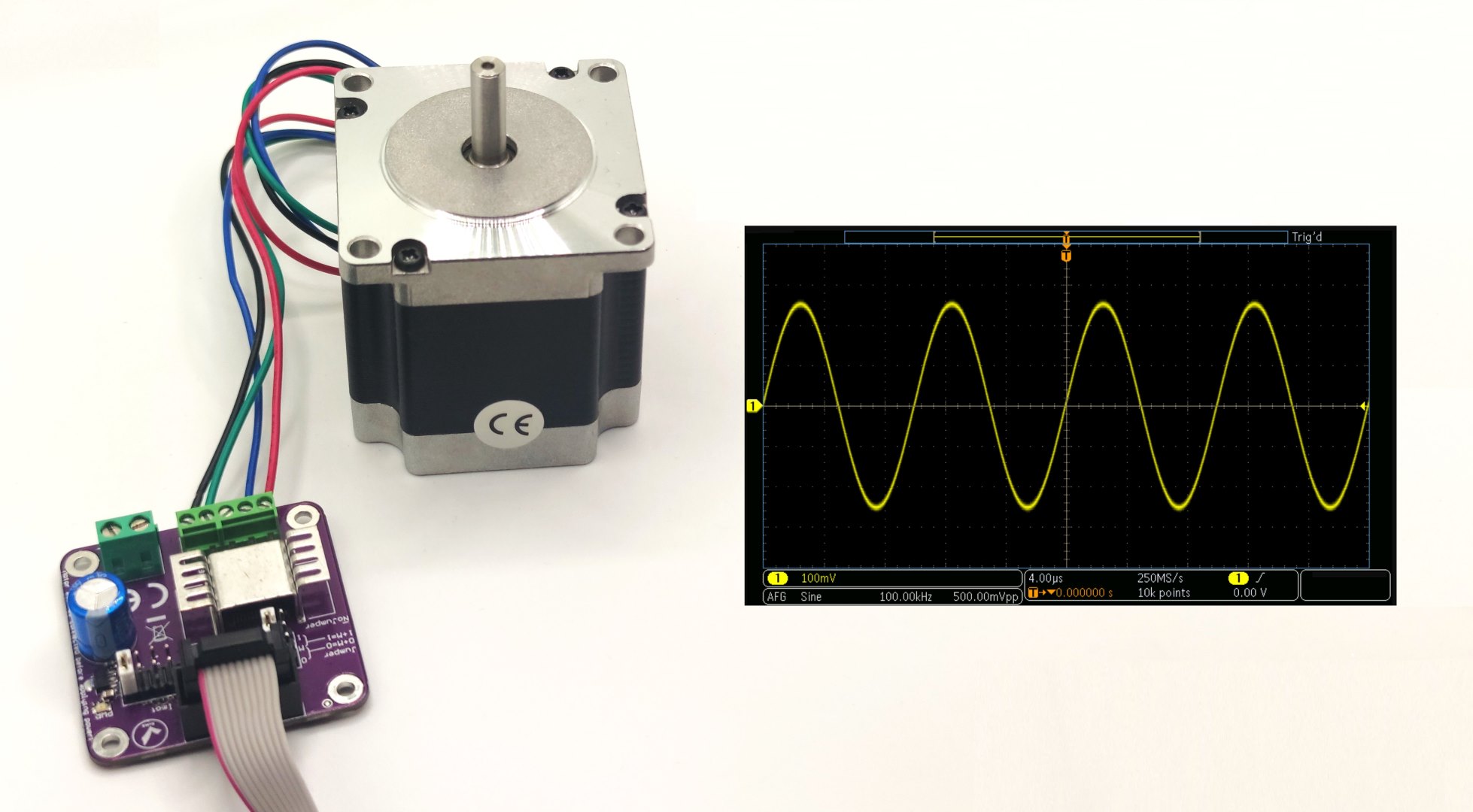
In summary, managing stepper motor current is crucial for optimizing performance, ensuring efficiency, and prolonging the motor’s lifespan. By understanding how current affects torque, heat generation, and power consumption, and by carefully adjusting and monitoring current settings, you can achieve reliable and effective motor operation in your automation systems.
Conducting Slip Ring Tests
Slip rings are vital components in systems that require continuous rotation while transmitting electrical signals or power from a stationary part to a rotating part. Commonly used in applications like wind turbines, rotary joints, and rotating machinery, slip rings facilitate uninterrupted electrical connections in rotating systems. Conducting slip ring tests is crucial for ensuring their reliability and performance.
What is a Slip Ring?
A slip ring, also known as a rotary electrical joint, consists of a rotating ring and a stationary brush. The brush makes contact with the ring, allowing electrical signals or power to be transferred while the ring rotates. This setup is essential for systems where continuous rotation is needed without interruption in electrical connectivity.
Importance of Slip Ring Testing
Regular testing of slip rings is essential for maintaining their functionality and ensuring that they meet performance standards. Slip ring testing helps identify potential issues such as wear, poor contact, or electrical noise, which can affect system performance and reliability.
Types of Slip Ring Tests
Electrical Continuity Test: This test checks whether the electrical connection between the rotating and stationary parts is continuous. Using a multimeter, you can measure the resistance across the slip ring contacts to ensure there is no significant resistance or breakage in the circuit.
Insulation Resistance Test: Insulation resistance tests assess the quality of insulation between different conductive parts of the slip ring. High insulation resistance values are crucial for preventing electrical shorts and ensuring safety. A megohmmeter is used for this test to measure resistance levels.
Wear and Mechanical Test: Mechanical tests evaluate the wear and tear on the slip ring components, such as brushes and rings. These tests often involve checking for signs of physical damage, scoring, or excessive wear that could impact performance. Regular inspection of these components helps prevent mechanical failures.
Signal Integrity Test: For applications requiring signal transmission, it is important to test the integrity of the transmitted signals. This involves verifying that the slip ring maintains signal quality without introducing noise or attenuation. Signal analyzers and oscilloscopes can be used for this purpose.
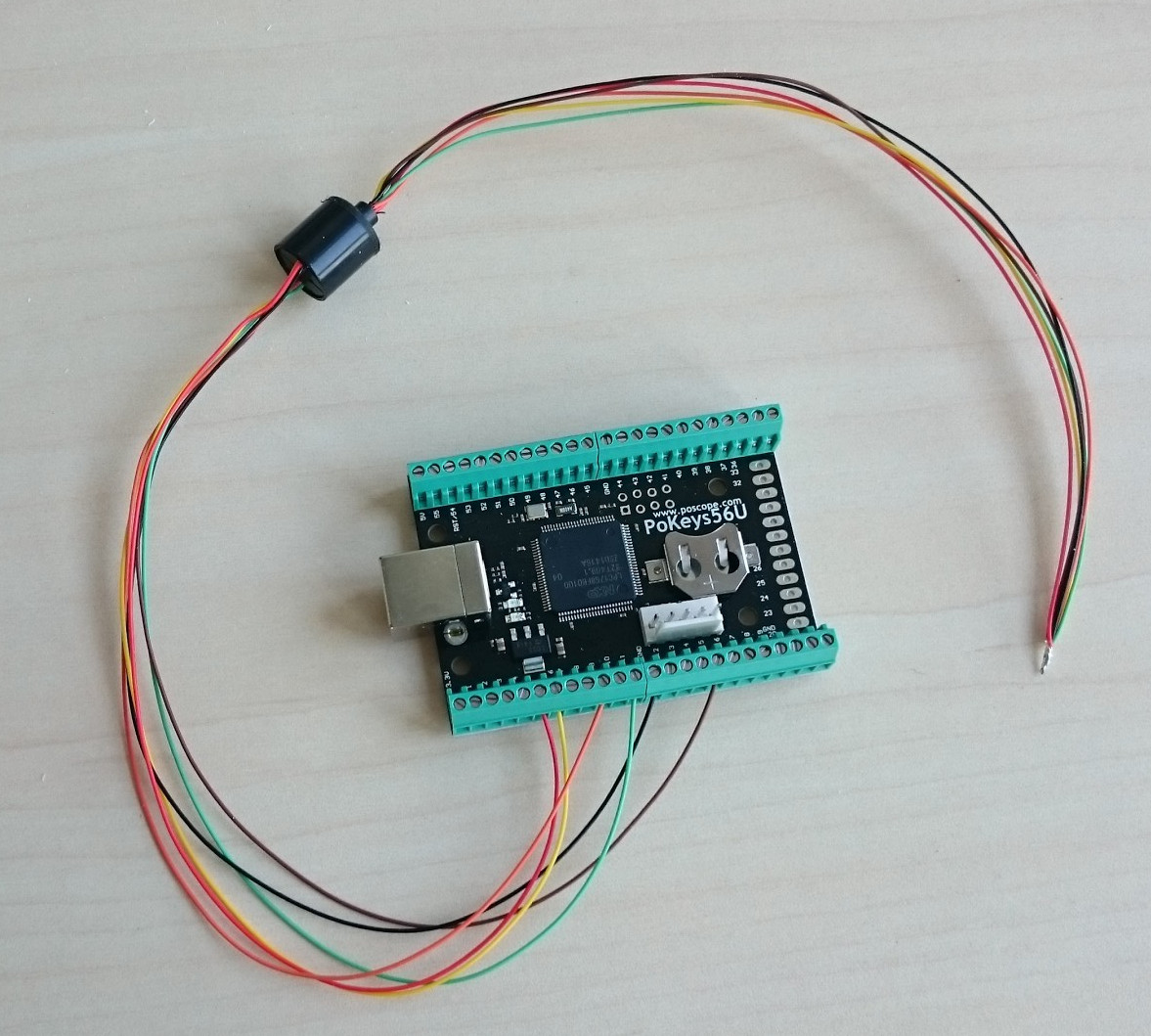
Conducting Effective Slip Ring Tests
Prepare Your Equipment: Ensure that you have the appropriate testing equipment, such as multimeters, insulation testers, and signal analyzers, ready and calibrated before beginning the tests.
Follow Testing Procedures: Adhere to standard procedures for each type of test. This includes properly setting up your equipment, performing tests in a systematic manner, and recording results accurately.
Analyze Results: Compare test results with the manufacturer’s specifications to determine if the slip ring is functioning correctly. Identify any deviations or issues that need to be addressed.
Maintain and Replace: Based on test results, perform necessary maintenance or replace components if significant issues are found. Regular maintenance helps ensure the longevity and reliable operation of the slip ring.
Common Issues and Solutions
Inconsistent Electrical Contact: If tests reveal intermittent contact, check for worn brushes or debris that may be affecting connectivity. Cleaning or replacing the brushes can often resolve this issue.
Insufficient Insulation: Low insulation resistance may indicate damaged insulation materials. Inspect and replace insulation as needed to restore proper electrical isolation.
Signal Distortion: If signal integrity tests show distortion, ensure that the slip ring contacts are clean and free from contaminants. Address any mechanical issues that may be affecting signal transmission.
In conclusion, slip ring testing is essential for ensuring the reliable operation of systems requiring continuous rotation. By conducting comprehensive tests—including electrical continuity, insulation resistance, mechanical wear, and signal integrity—you can identify and address potential issues, thereby maintaining the performance and longevity of your slip rings. Regular testing and maintenance will help prevent unexpected failures and ensure smooth, uninterrupted operation in your rotating systems.
Read more:
- Understanding Essential Components for Advanced Electronics Projects
- The Mach4 CNC Controller | An overview and integration with PoKeys57CNC, Mach3 limit switches and tutorials
Conclusion
In summary, the effective operation of stepper motors and their associated components—stepper motor drivers, Modbus stepper drivers, stepper motor current management, and slip rings—is crucial for achieving high performance and reliability in automation systems.
Stepper Motor Drivers are fundamental for controlling the precise movement and positioning of stepper motors. They convert digital pulses into the necessary electrical signals, influencing torque, speed, and overall performance. Selecting the right driver and configuring it correctly is essential for optimal motor operation.
Modbus Stepper Drivers enhance the functionality of stepper motor drivers by integrating the Modbus communication protocol. This allows for centralized control, real-time monitoring, and scalable system design. Leveraging Modbus capabilities can significantly improve the coordination and efficiency of complex automation systems.
Stepper Motor Current management is critical for balancing torque production with heat generation and power consumption. Properly setting and adjusting the current based on motor specifications helps avoid overheating, ensures efficient performance, and extends the motor’s lifespan.
Slip Ring Testing is vital for systems that require uninterrupted electrical connectivity during rotation. Regular testing for electrical continuity, insulation resistance, mechanical wear, and signal integrity helps identify and address potential issues, ensuring the reliability and longevity of slip rings in your applications.
Understanding and managing these components and their interactions can significantly impact the success of your automation projects. By applying best practices in driver selection, current management, and slip ring testing, you can achieve enhanced performance, reliability, and efficiency in your systems.